Custom jewelry packaging can start from many details, such as printing plate making, processing technology, materials used, etc. Most brand jewelers will choose custom jewelry packaging.
A good design plan should adopt suitable process conditions to achieve the expected effect. As a jewelry packaging designer, not only must master the design rules and application software, but also master the process and principles of packaging and printing. Learn to use it to make the design meet the production requirements, and under the limited process conditions, give full play to your expressive power, so as to facilitate plate making and printing, reduce the number of printing workers, save the number of editions, and shorten the working hours, while achieving the desired effect. , and save the production cost.
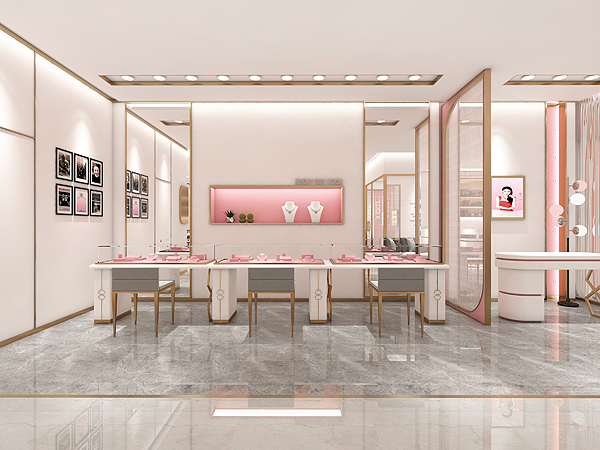
What are the steps for custom jewelry packaging printing plate making?
1. Scanning and electronic color separation
When creating custom jewelry packaging, it is impossible for all materials to be original. Many materials can be obtained by shooting, copying originals, etc. Since there are many types of originals in plate making, such as positives and negatives, prints, photos, etc., in order to accurately When these materials are applied to packaging design, it is necessary to separate these materials, that is, to decompose the three primary colors CMY that make up the color, and then synthesize them into the packaging through the printing machine. According to the principle of lighting during color separation, manuscripts can be divided into two types: reflective manuscripts and transmissive manuscripts. The original is opaque, we call it reflective. In color separation, when the light source irradiates the original, it will be reflected back, using the principle that the reflected light of different colors is also different to carry out reflective scanning color separation. Reflections include photographs, prints, hand-drawn manuscripts, and other images. The original transmission manuscript is transparent, and the back side of the manuscript is irradiated by a light source, and the image is formed by using the transmitted light. The positive film, negative film, etc. mentioned above are all transmission manuscripts.
(1) scan
Scanning is the most common color separation method. It mainly uses digital processing to perform RGB color separation processing on reflective drafts and transmission drafts, and then convert them into CMYK mode for printing through software. General scanners have their own image processing system, and some can directly get CMYK mode. However, in order to separate the colors accurately, it is still necessary to draw them into RGB and then use Photoshop to process them.
(2) electronic color separation
If the image quality requirements are relatively high, it is necessary to carry out electronic color separation processing on the original. The principle is to paste the original on the cylinder of the electronic colorimeter and scan it through a photomultiplier tube. When the instrument is rotated, the pixels of the image are extracted and separated one by one, and the optical signal is replaced with the corresponding analog electrical signal. The electronic circuit is used to correct the signal, and finally, the corrected electrical signal is restored to an optical signal, and the desired color separation image is input into the computer in the way of point-by-point exposure. The color of the image obtained by the electronic division is very accurate, and the original can be almost perfectly restored. In addition to scanners and color separation machines, digital camera shooting is also a common color separation method, but the color reproduction of the originals that are shot with a digital camera is much poorer.
2. Jewelry packaging plate making
Taking offset printing as an example, the general process of jewelry packaging box printing is designed finalization → imposition of output film → making PS version → on-machine printing → various post-printing processes → finished product warehousing or shipment. That is, when the design is approved by the customer, it can be delivered to the printing house for printing and production. Although most of the time after submitting the confirmed design draft, the design work is completed, understanding the printing process flow can meet the requirements of packaging printing design and make the design a reality.
(1) Imposition
The imposition is to repeatedly arrange the designer's design draft on a full-page paper through an imagesetter and typesetting software so that the full-page printing can save costs. Jewelry packaging printing generally adopts whole and folio printing. During the imposition process, pay attention to the size requirements of the printing machine biting the paper.
(2) Filming
After the imposition is completed, the film can be produced by the photos better. In the printing operation, a full-color image (in CMYK mode)
needs to be colored by four inks, so there are four color versions, and the imagesetter can directly output the files sent from the computer to generate four CMYK color separation films. When four-color printing cannot meet the requirements, or when four-color printing is not desired to save costs, it is necessary to use spot-color printing. A spot color only needs to produce a one-color version, and there is no need to produce four versions like four-color printing.
(3) Proofreading
After the film is finished, check the film for errors and discrepancies with the design documents, so as to find the problem in time, make changes to the film, or re-produce the film.
(4) Proofing
The finished printing plate is installed on the proofing machine for trial printing, which is called proofing. Proofing is the last comprehensive proofreading of the design files that have been imposition and output to film before printing. It is a reconfirmation of the image and text position and color effect. It is an advance preview of the final printing effect. Technical basis and reference values. The proofing paper should generally use the same paper as the formal printing so that the final printing effect can be previewed more accurately.
(5) Printing
After the film is confirmed to be correct by proofing, it can be printed and ready for printing. The printing is to cover the film on the surface of the aluminum plate coated with the photosensitive liquid (PS version) and expose it to the printing machine. The exposure time is determined by the density and transparency of the film, the thickness of the lines, and the properties of the photosensitive liquid. One version of each of the four CMYK films, for a total of four versions, if there is a spot color, an additional version is required. The light sources used for printing are generally xenon lamps rich in blue and violet light, high-pressure mercury lamps, and carbon lamps. The layout output of the copy printing is the positive image of the positive image, the blank part is white, and the next part shows the same shades as the original image.
(6) Development
The sun-baked version cannot be printed on the machine immediately, and special treatment should be performed on the layout so that the blank part forms a stable hydrophilic film layer such as metal inorganic salt or metal oxide, and the graphic part forms a stable fatty acid or hardened photosensitive resin hydrophilic film. The oil layer improves the adsorption capacity of the printing plate to water and ink.
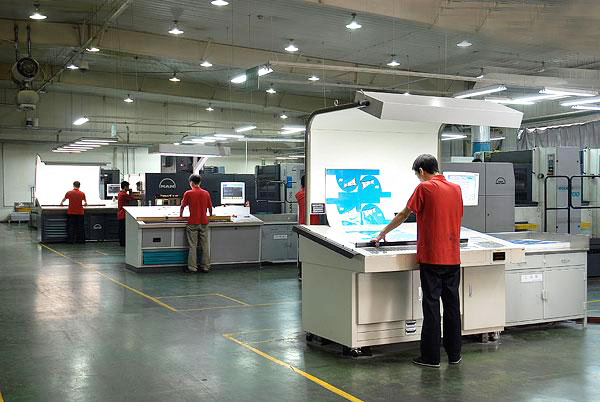
What processing techniques are used for custom jewelry packaging?
The jewelry packaging and printing factory can prepare for printing, check the machine, mix the ink, and apply the PS version to the trial printing. The trial printing is mainly to check and adjust the transmission effect of the paper, the pressure of the pressure roller, and whether the ink color meets the requirements. When the machine fully meets the printing requirements, it can be officially printed in large quantities, and then go through the post-printing process, such as embossing, die-cutting, folding, and forming, to complete the entire production process of packaging.
1. Printing
During printing, the printing plate fixed on the printing plate cylinder undergoes the moisturizing and ink feeding process. On the treated printing plate, the principle of the immiscibility of oil and water is used to make the ink and text parts water-repellent and the blank part hydrophilic. Repel ink, transfer the positive positive image on the plate to the rubber of the transfer roller to form a positive-negative image, and then the positive-negative image on the rubber is embossed on the paper by the embossing roller to get a Clear print.
2. Coating and glazing
In order to enhance the wear resistance, anti-fouling function, and visual effect of the printed parts, lamination and varnishing technology are usually required to improve the quality of the printed parts and enhance the function.
(1) Lamination
Also known as plastic sticking, the method is to press and stick a certain thickness of plastic film on the printed piece through the hot pressing device of the special plastic sticking machine, so that the printed piece and the plastic film are compounded together. After lamination, the surface of the printed piece is smoother and brighter, thereby improving the gloss and firmness of the printed matter, the color of the picture and text is more vivid, and it is full of three-dimensional effects.
(2) Glazing
The methods of glazing can be divided into two types: partial glazing and comprehensive glazing. Partial glazing is mostly used in the parts that need to be highlighted, suitable for the cover of books, packaging boxes, etc., to make the picture more three-dimensional. Full glazing can increase the brightness of the paper surface and the degree of wear resistance of the print. Most of the covers of books and periodicals use comprehensive glazing technology.
3. Die-cutting and embossing
The paper cutter can only cut straight lines. When printed materials such as jewelry packaging require circular arcs, windows, creasing lines, and irregular curves, they must be processed by die-cutting. Embossing on glass or plastic surfaces is an integral part of the molding process.
4. In-mold labeling of plastic packaging structures
Pressure-sensitive labels, sizing labels, heat-shrinkable sleeve labels, heat transfer foil layers, and decals are all traditional methods of labeling and decorating injection molding and glass bottles. The above-mentioned steps are usually carried out after the manufacture of these containers (ie, after forming). In-mold labeling is a pre-decorated process that can be used for both blow-mode and injection-mode packaging of bottles and packaging containers.
5. Ceramic labels for glass packaging structure
Ceramic labeling (ACL) is another processing technology with a "no label" appearance. The specific method is to attach a mixture of ceramic powder and thermoplastic chemical material (which turns into ink when heated) by screen printing on glass. the surface of the container.
The above is a detailed introduction to the printing plate making and processing technology of customized jewelry packaging. If you have any questions, please contact us!